What is Sheet Metal Stamping?
Sheet metal stamping is a manufacturing process in which sheet metal is cut and formed into a desired shape or profile. It is commonly used to produce a variety of parts, such as car panels, cooking utensils, and aircraft wings.
In sheet metal stamping, a sheet metal blank is placed on a stamping press, which consists of a stationary bed and a sliding ram. The blank is held in place by a clamping mechanism, while a stamping tool, or die, is brought down onto the blank by the ram. The die is shaped like the final part and contains a cavity that matches the shape of the part. As the ram moves downward, it applies pressure to the blank, causing it to deform and take on the shape of the cavity in the die.
There are several different types of sheet metal stamping processes, including blanking, piercing, and forming. Blanking involves cutting the sheet metal into a specific shape, while piercing involves creating a hole or opening in the metal. Forming involves bending or deforming the metal into a specific shape without cutting it.
Sheet metal stamping is a cost-effective and efficient way to produce large quantities of parts with a high degree of accuracy and consistency. It is widely used in the automotive, aerospace, and electronics industries, among others.
Sample Sheet Metal Stamping Parts:
Machines & Equipment Used in Sheet Metal Stamping?
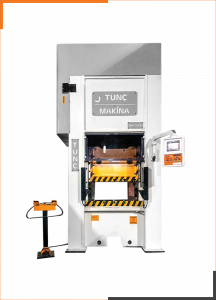
There are several types of machines that are commonly used for sheet metal stamping, including:
- Stamping press: This is the primary machine used for sheet metal stamping. It consists of a stationary bed and a sliding ram, which moves up and down to apply pressure to the sheet metal blank. The stamping press can be mechanical, hydraulic, or pneumatic, depending on the type of power used to drive the ram.
- Stamping Die: The die is a tool that is used to shape the sheet metal during the stamping process. It is typically made of high-strength steel and is custom-designed to match the desired shape of the final part. The die is mounted on the stamping press and is brought down onto the sheet metal blank by the ram.
- Punch: The punch is a tool that is used to cut or form the sheet metal during the stamping process. It is typically made of high-strength steel and is custom-designed to match the desired shape of the final part. The punch is mounted on the stamping press and is brought down onto the sheet metal blank by the ram.
- Transfer press: A transfer press is a type of stamping press that is used to produce parts with more complex shapes or features. It consists of a series of stations, each of which performs a different operation on the sheet metal blank. The blank is transferred from one station to the next by a series of mechanisms, such as gears or cams.
- Coil line: A coil line is a machine that is used to unroll a coil of sheet metal and feed it into a stamping press. It consists of a series of rollers that support and guide the sheet metal as it is fed into the press. The coil line can also include additional equipment, such as straighteners, levelers, and shears, which help to prepare the sheet metal for the stamping process.
Types of Sheet Metal Stamping Presses:
There are various types of stamping presses that are used in the sheet metal stamping process, including:
- Mechanical stamping press: This type of press uses a mechanical flywheel and clutch system to generate the force needed to stamp the sheet metal. The flywheel stores energy as it is rotated and then releases it in a controlled manner to drive the ram.
- Hydraulic stamping press: This type of press uses a hydraulic system to generate the force needed to stamp the sheet metal. The system consists of a pump, valves, and cylinders, which convert hydraulic fluid pressure into mechanical force.
- Pneumatic stamping press: This type of press uses compressed air to generate the force needed to stamp the sheet metal. The press has a compressor that generates the air pressure, which is then stored in a tank and released through a valve to drive the ram.
- Servo press: This type of press uses a servo motor to drive the ram, which allows for precise control of the stamping process. The servo press is typically used for high-precision applications, such as producing microelectronic components.
- Transfer press: A transfer press is a type of stamping press that is used to produce parts with more complex shapes or features. It consists of a series of stations, each of which performs a different operation on the sheet metal blank. The blank is transferred from one station to the next by a series of mechanisms, such as gears or cams.
What are the Types of Metal Stamping Dies?
There are several types of sheet metal stamping dies that are used in the manufacturing process, including:
- Progressive die: A progressive die is a type of stamping die that is used to produce parts with multiple features or operations. It consists of a series of stations, each of which performs a different operation on the sheet metal blank as it progresses through the die. The blank is fed into the die by a coil line and is then shaped and cut by a series of punches and dies.
- Compound die: A compound die is a type of stamping die that is used to produce parts with complex shapes or features. It consists of two or more dies that are used in conjunction with each other to form the sheet metal. The dies may be mounted on the same stamping press or on separate presses.
- Draw die: A draw die is a type of stamping die that is used to produce parts with deep or complex shapes, such as cups or containers. It consists of a punch and a die that are used to stretch the sheet metal into the desired shape.
- Punch and die: A punch and die set is a basic stamping die that consists of a punch and a die. The punch is used to cut or form the sheet metal, while the die provides a backing for the punch to press against. Punch and die sets are used to produce simple parts with a limited number of features.
- Forming die: A forming die is a type of stamping die that is used to bend or deform the sheet metal into a specific shape without cutting it. It may consist of a single die or a series of dies that are used to shape the metal in stages. Forming dies are commonly used to produce parts with complex shapes or features.
How to Design Stamping Dies?
There are several steps involved in designing sheet metal stamping dies:
- Determine the desired shape and dimensions of the final part: The first step in designing a stamping die is to determine the desired shape and dimensions of the final part. This may involve reviewing engineering drawings, customer specifications, or sample parts.
- Select the appropriate material for the die: The next step is to select the appropriate material for the die. Common materials used for stamping dies include tool steel, carbide, and ceramic. The material selection will depend on the type of stamping process being used, the properties of the sheet metal, and the required level of precision and wear resistance.
- Create a 3D model of the die: The next step is to create a 3D model of the die using computer-aided design (CAD) software. The model should include all of the features and dimensions of the die, as well as the locations of the punches and dies.
- Analyze the stamping process: The next step is to analyze the stamping process to ensure that the die will function correctly. This may involve simulating the stamping process using finite element analysis (FEA) software to predict the forces and stresses that will be applied to the die.
- Fabricate the die: Once the design of the die has been finalized, it can be fabricated using a variety of methods, such as milling, grinding, or EDM (electrical discharge machining). The die may be machined from a solid block of material or may be built up using multiple layers of material.
- Test and refine the die: After the die has been fabricated, it should be tested to ensure that it functions correctly and produces parts that meet the desired specifications. If necessary, the die can be refined or modified to improve its performance.
Which Softwares are used in Sheet Metal Stamping Die Design?
There are many CAD/CAM software programs that are commonly used to design stamping dies, including:
- SolidWorks: SolidWorks is a popular 3D modeling software that is widely used in the manufacturing industry. It has a range of tools and features that are specifically designed for designing stamping dies, such as the ability to create 3D models of the die, simulate the stamping process, and generate accurate 2D drawings and manufacturing documentation.
- AutoCAD: AutoCAD is a well-known 2D and 3D drafting and design software that is widely used in the manufacturing industry. It has a range of tools and features that can be used to design stamping dies, such as the ability to create precise 2D drawings, generate 3D models of the die, and create manufacturing documentation.
- Siemens NX: Siemens NX is a comprehensive CAD/CAM software that is widely used in the manufacturing industry. It has a range of tools and features that are specifically designed for designing stamping dies, such as the ability to create 3D models of the die, simulate the stamping process, and generate accurate 2D drawings and manufacturing documentation.
- Pro/ENGINEER: Pro/ENGINEER is a 3D modeling and design software that is widely used in the manufacturing industry. It has a range of tools and features that are specifically designed for designing stamping dies, such as the ability to create 3D models of the die, simulate the stamping process, and generate accurate 2D drawings and manufacturing documentation.
- Inventor: Inventor is a 3D modeling and design software that is widely used in the manufacturing industry. It has a range of tools and features that are specifically designed for designing stamping dies, such as the ability to create 3D models of the die, simulate the stamping process, and generate accurate 2D drawings and manufacturing documentation.
Is Sheet Metal Stamping a Productive Process?
Sheet metal stamping is a highly productive manufacturing process that is capable of producing large quantities of parts with a high degree of accuracy and consistency. It is widely used in a variety of industries, including automotive, aerospace, and electronics, to produce a variety of parts, such as car panels, cooking utensils, and aircraft wings.
One of the key benefits of sheet metal stamping is that it allows for the production of parts with a high level of complexity and precision. The process can be used to produce parts with a wide range of shapes and features, including holes, slots, and bends, and can achieve tolerances as low as 0.005 inches.
Another benefit of sheet metal stamping is its efficiency. The process can produce parts at a high rate of speed, with some stamping presses capable of producing hundreds or even thousands of parts per minute. This makes it an ideal choice for high-volume production runs.
Overall, sheet metal stamping is a highly productive and efficient manufacturing process that is widely used to produce a wide range of parts with a high level of precision and accuracy.
Is Turkey the Right Country for Ordering Stamped Parts?
Turkey has a well-developed manufacturing sector and is known for producing a variety of metal parts and products, including sheet metal stamped parts and dies. It has a strong base of skilled labor and a favorable business environment, which makes it an attractive location for companies looking to outsource their manufacturing.
Turkey has a number of advantages when it comes to sheet metal stamping, including:
- Competitive labor costs: Turkey has lower labor costs compared to many other countries, which can help to reduce the overall cost of production.
- Advanced manufacturing capabilities: Turkey has a well-developed manufacturing sector and is home to a number of advanced manufacturing facilities that are equipped with the latest technology and equipment.
- Strong supply chain: Turkey has a well-established supply chain that can help to ensure the timely delivery of raw materials and finished products.
- Strategic location: Turkey is located at the crossroads of Europe, Asia, and the Middle East, which makes it an ideal location for companies looking to serve these markets.
Overall, Turkey is a good place to consider for companies looking to order sheet metal stamped parts and dies. However, it is always important to thoroughly research and evaluate any potential supplier to ensure that they can meet your specific needs and requirements.
What to Look for When Choosing a Sheet Metal Stamping Company?
When looking for a sheet metal stamping company in Turkey, it is important to do your research and consider a number of factors, such as:
- Capabilities: Make sure that the company has the capabilities to meet your specific needs and requirements. This may include the types of stamping processes they offer, the materials they can work with, and the size and complexity of the parts they can produce.
- Quality: Look for a company that has a strong track record of producing high-quality parts and has the quality control systems in place to ensure that their products meet your specifications.
- Capacity: Consider the company’s capacity to meet your production needs. This may include the size of their facility, the number of stamping presses they have, and their ability to scale production as needed.
- Location: Consider the company’s location and whether it is convenient for shipping and logistics.
- Price: Price is always an important factor, but be sure to consider the overall value of the supplier, including the quality of their products, their delivery reliability, and their customer service.
Overall, it is important to thoroughly research and evaluate potential suppliers to ensure that they can meet your specific needs and requirements.